SAFE & RELIABLE
Pressure and temperature measurement technology for hydrogen processes
We at Labom have been building devices for hydrogen applications for over 20 years. With the help of our hydrogen calculation tool and our numerous different process connections, we can define and produce customised and individual measuring devices - and thus find the right measuring solution for every application.
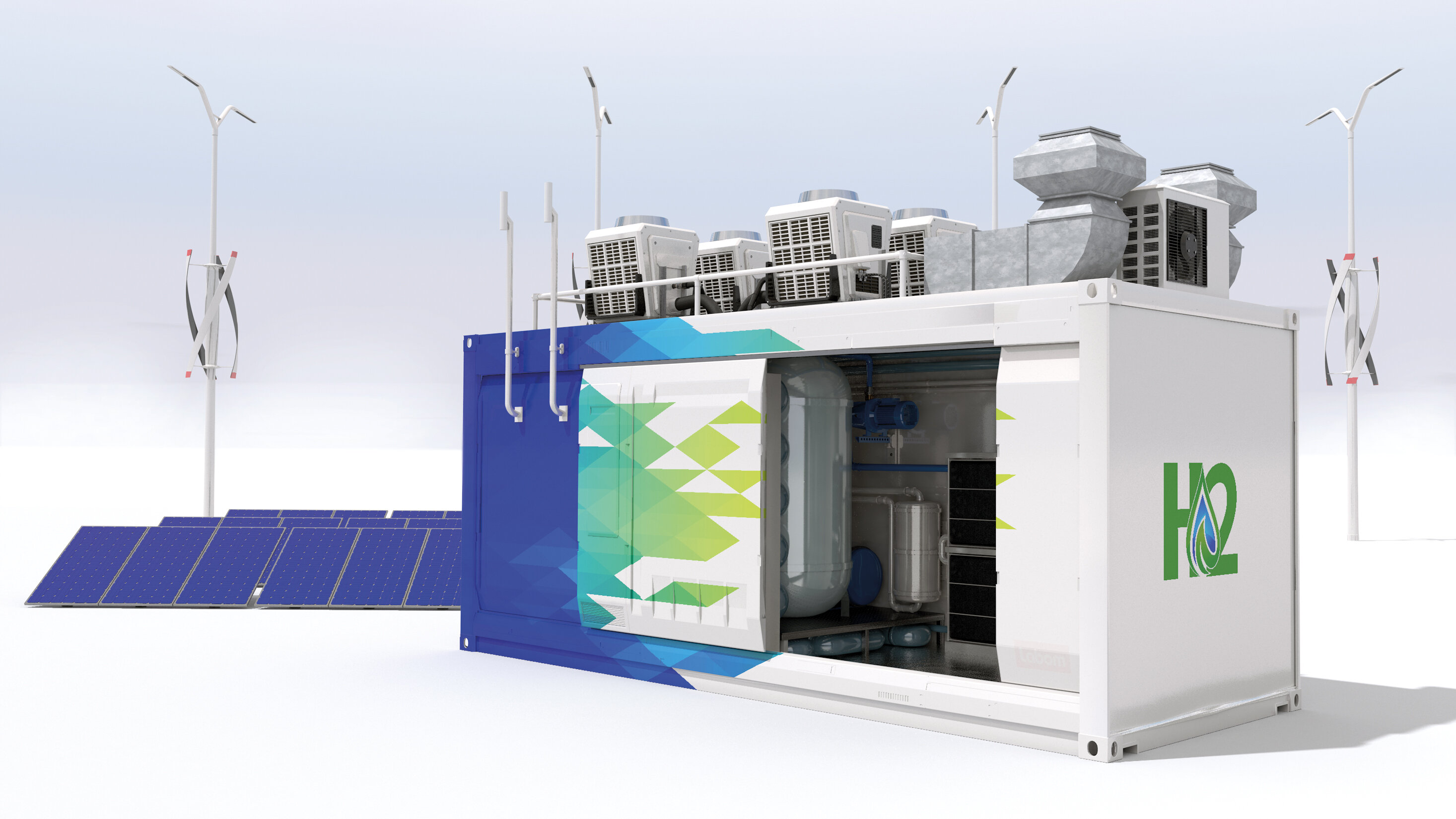
Elektrolysis
The hydrogen of the future is known as green hydrogen. As renewable energy sources are used to electrolyse water in its production, it is climate-neutral – it can also be produced in large volumes. During the electrolysis, water (H2O) is split into hydrogen (H2) and oxygen (O ). There are currently various types of electrolysers, these include alkaline electrolysers that use potassium hydroxide solution as the electrolyte, PEM electrolysers that use a proton membrane to separate the hydrogen and oxygen, and solid oxide electrolyser cells (SOEC) that split water vapour at temperatures of up to 850°C. What all these have in common is that they set high demands on the measuring devices used, which must reliably measure high temperatures, pressure and fill levels, and should be as simple as possible to install and monitor.
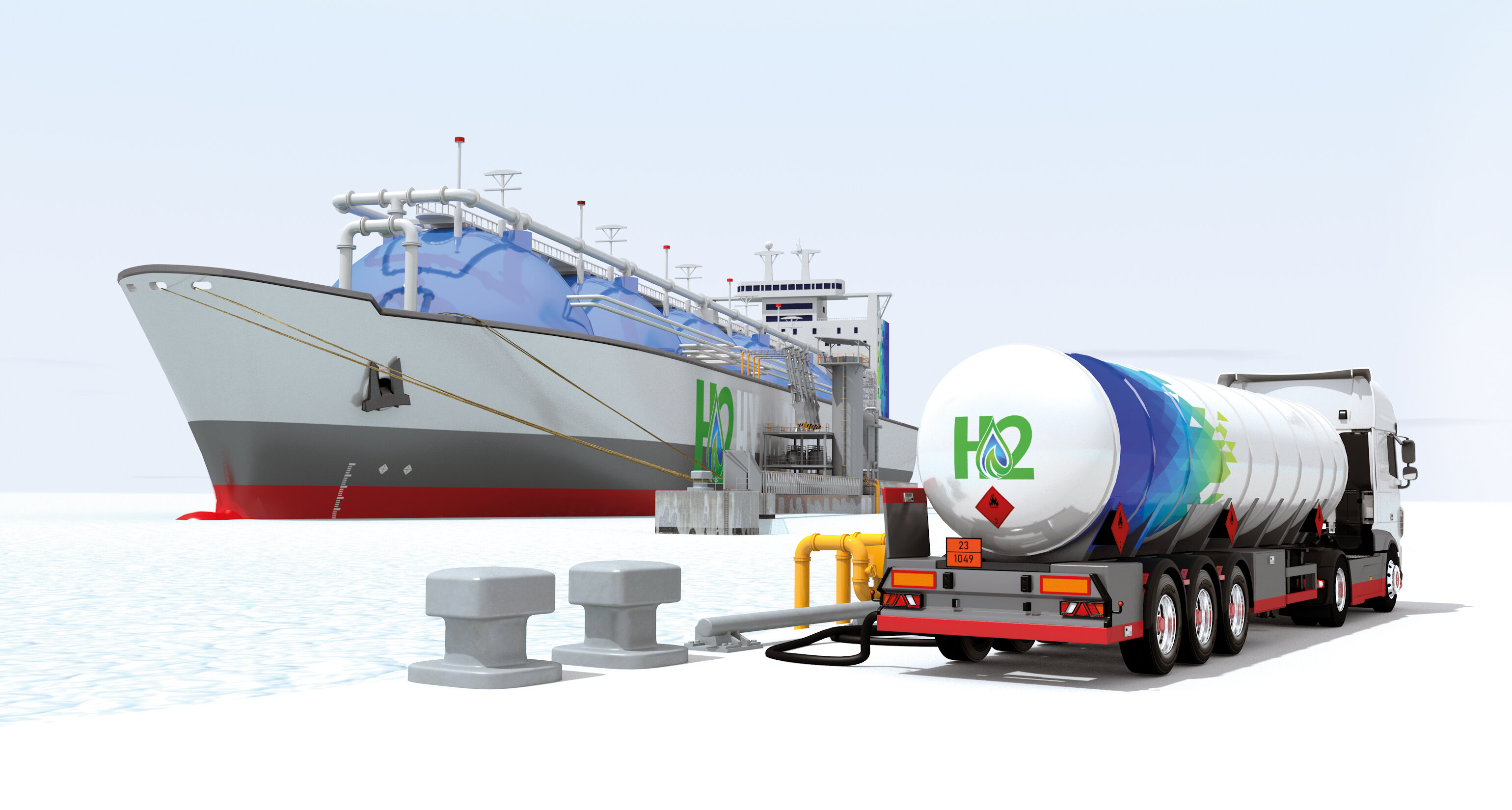
Storage and transportation
Hydrogen has a particularly high energy density compared to other fuels. However, at normal temperatures and air pressure, the energy of hydrogen is distributed over a larger volume. Special solutions are therefore required for its storage and transportation. For example, gaseous hydrogen is stored for transport or at fuelling stations in containers with high pressures of up to 1,000 bar in order to minimise the volume. On the other hand, liquid hydrogen, which has a smaller volume, is maintained at cryogenic temperatures of -253°C, but can be stored at 1 bar. As the auto-ignition temperature of hydrogen is lower than that of other substances, reliable measurement technology is crucial to avert this potential hazard.
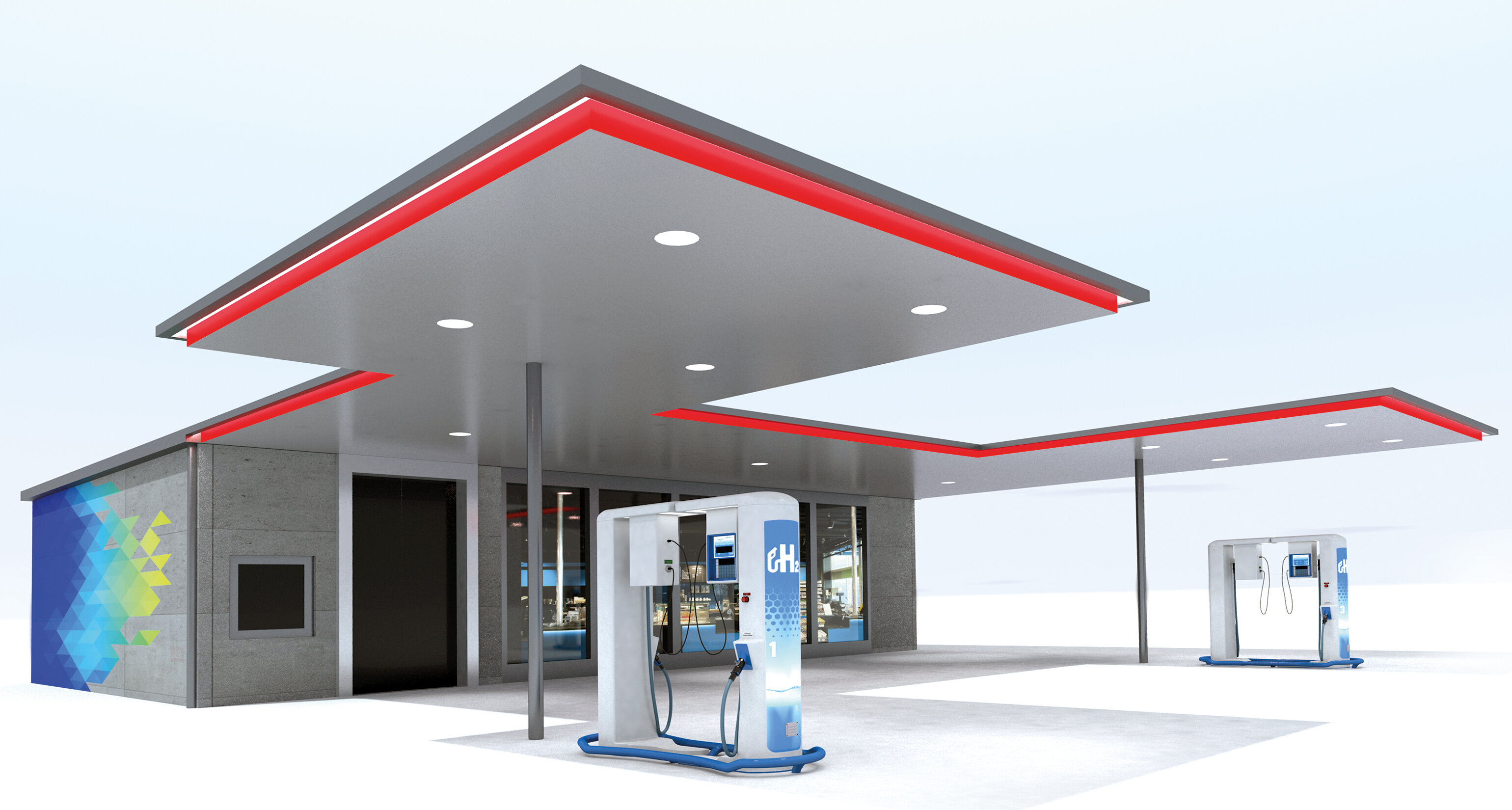
Hydrogen fuelling stations
At hydrogen fuelling stations, vehicles are refuelled with hydrogen that is stored in liquid or gaseous form. The system usually consists of storage tanks that are maintained at constant pressures and temperatures as well as compression equipment for medium to high-pressures up to 900 bar, a cooling element that cools the hydrogen to -40°C before it is pumped into the vehicle, and the fuel pump itself. To cater for these differing needs, a range of measuring devices is required at hydrogen fuelling stations to monitor the temperature, pressure and filling levels – for which special certifications such as approval for explosion protection are advisable, due to the particularly high safety requirements.
Hydrogen for energy storage
The variable nature of renewable energy is considered one of the greatest challenges in implementing the energy transition: Solar and wind sources cannot be regulated according to the needs of electricity customers at any given time. The development of workable and economic power storage technologies is therefore a decisive factor for success of the energy transition. Labom is at home both in the equipping of wind turbines in close cooperation with leading manufacturers and in the energy storage segment in terms of metrology.
Hydrogen plays a key role in the storage of surplus energy. Surplus energy from renewable energy sources can be used to produce hydrogen via electrolysis in order to store the energy. Hydrogen is also the initial medium for Power2X processes. Nevertheless, handling the smallest molecule in existence also presents a challenge: Hydrogen dissolves in numerous metals and is so small that it penetrates stainless steels and causes some types of steel to become brittle.
Our H2-Products
5 product series & 100+ process connections
For over 20 years the company LABOM Mess- und Regeltechnik, based in the northern German town of Hude, has been making measuring devices for hydrogen applications. Drawn from this experience, LABOM has developed several series of pressure transmitters that can be used in both standardised and application-defined hydrogen processes. The measuring instruments of the PASCAL CV4 and PASCAL Ci4 series as well as COMPACT CA16 cover a measuring range between -1 and 1050 bar, depending on the capabilities of the individual pressure transmitter, can be used down to -40°C and are also certified with Ex-protection and some with SIL. Hydrogen-proof stainless steels are used for the wetted parts, as well as polymers suited to hydrogen, such as NBR, EPDM and PVDF.
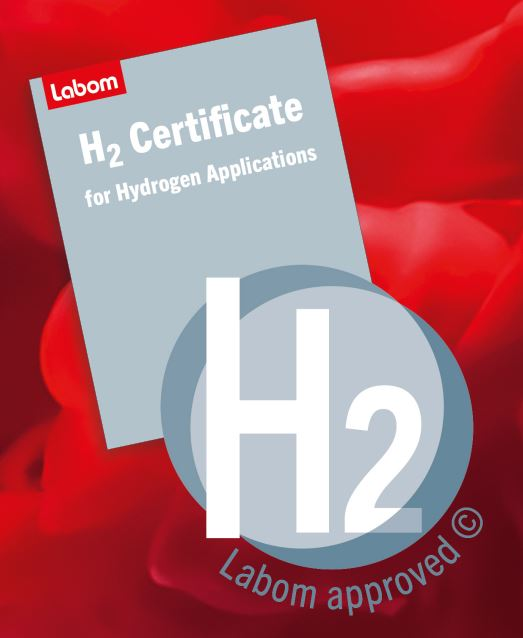
On request: Certificate for H2 suitability of pressure gauges can be ordered.
Our hydrogen certificate is issued specifically according to the details of your individual instrument configuration as well as the requirements of your application conditions. Based on the process parameters you provide, such as pressure, temperature and hydrogen concentration, we calculate the time period within any potential negative effects of hydrogen on the measuring device can be safely excluded. This confirmation is provided to you in the form of a certificate which can also be used for inspections.
The Labom H2-Calculation tool
Calculation of the hydrogen resistance of measuring instruments
Hydrogen penetrates stainless steel. This effect can have negative influences on the function of measuring instruments. With our hydrogen tool, we can calculate the time period in which this effect is reliably excluded for measuring instruments with diaphragm seal systems, depending on the most important influencing factors.
Hydrogen embrittlement
When hydrogen atoms migrate through metals, they disrupt the crystal lattice, causing the material of commonly used alloys to become brittle. Choosing the right material is therefore crucial. However, hydrogen-resistant stainless steels are precisely those that are less springy and therefore only have limited application in technology for pressure measurement. One solution can be an upstream diaphragm seal.
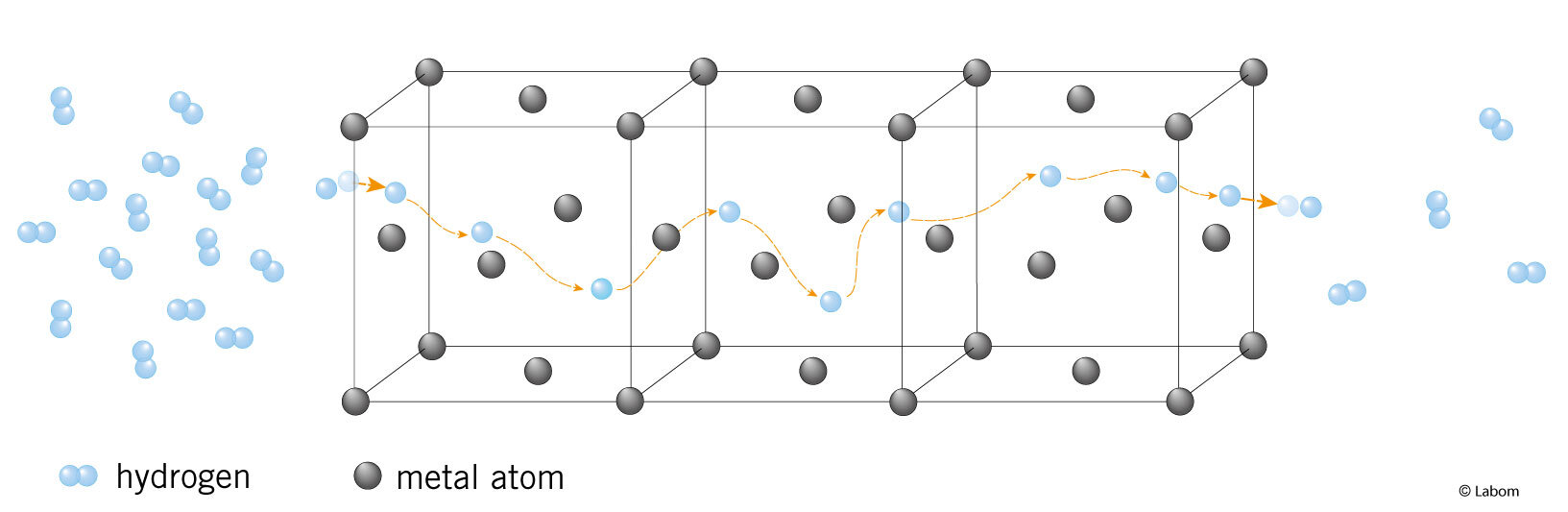
Hydrogen permeation through stainless steel
The hydrogen molecule decomposes into hydrogen atoms on the surface of metals and these can diffuse through metals: First the hydrogen molecules decompose into atoms, then the atoms migrate through the tetrahedral and octahedral gaps of the metal lattice and reunite as molecules on the other side. The whole process is called permeation (see illustration).
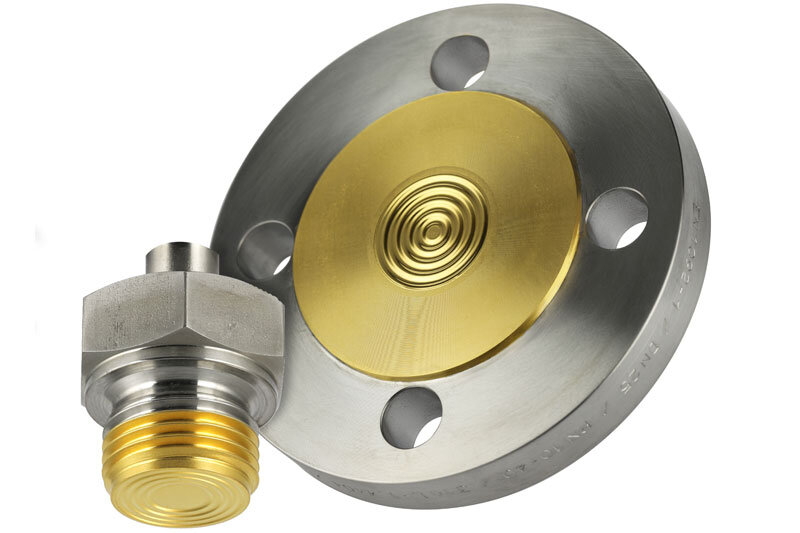
Influence on pressure measurement technology
Diaphragm seals have a thin metal diaphragm on the process side. The pressure is transmitted to the sensor via the diaphragm and a filling liquid, usually oil. If hydrogen penetrates the membrane, it dissolves in the oil. Once saturation is reached, the hydrogen forms beads as the pressure is relieved and this leads to measurement errors such as shifting the zero point